I remember the first time I submitted a shoe design to a factory. I was excited—until the email came back. “Pattern needs adjustments. Won’t produce as is.” My heart sank. I had spent weeks perfecting the design, but without a proper pattern, it was useless.
That’s when I realized something: a great design means nothing if the pattern isn’t production-ready.
I had to relearn everything, from how materials stretch to how different factories interpret measurements. It wasn’t easy, but once I figured it out, things changed. Samples came back right the first time. No more costly revisions. No more delays.
If you’re a brand owner or retailer looking to take control of your production, you need a pattern that works.
This guide will walk you through each step, from concept to factory-ready design.
By the end, you’ll know exactly how to create patterns that factories can actually use—without the frustration I went through.
So let’s start!
1. What are Shoe Patterns?
A shoe pattern is the technical blueprint used to cut and assemble materials into a finished shoe. Think of it as the foundation of footwear manufacturing—every shoe you see on the market starts with a pattern.
A good pattern influences:
- Fit: A precise pattern ensures that every size maintains proper proportions.
- Style: The pattern dictates the shoe’s shape, structure, and visual appeal.
- Durability: Well-designed patterns prevent weak points that lead to wear and tear.
The Relationship Between Pattern Making & Shoe Quality
A poorly made pattern affects more than just aesthetics—it impacts comfort, durability, and even customer satisfaction.
How a well-made pattern improves quality:
- Enhances ergonomic fit, reducing discomfort and pressure points.
- Strengthens structural integrity, preventing weak seams and early breakdown.
- Reduces manufacturing errors, leading to a lower defect rate.
Shoe patterns are more than just technical drawings. They are the foundation of quality, consistency, and efficiency in footwear production. At XDS, we make sure that before producing shoes, we have a well-prepared shoe pattern to guarantee precision, consistency, and optimal material usage, ensuring high-quality footwear production.
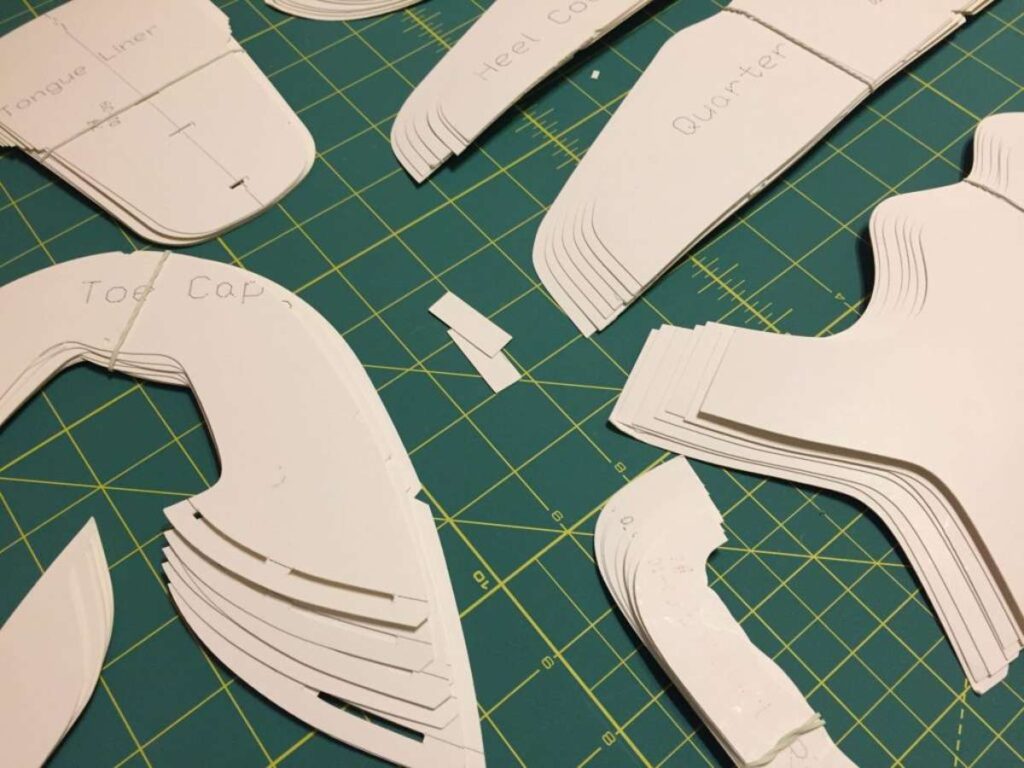
2. Steps on How To Make a Shoe Pattern?
Shoe pattern-making is both a technical process and an art. If the pattern isn’t right, production will be full of delays, rejections, and costly adjustments. But when done correctly, it streamlines manufacturing, minimizes waste, and keeps customers happy with consistent sizing.
So how do you create a shoe pattern that works for mass production? Whether you’re designing for sneakers, heels, or boots, the process starts with one crucial element—the shoe last.
Here are the detailed steps:
Step #1 Choosing the Right Shoe Last
A shoe last is the 3D mold that shapes a shoe’s fit, structure, and overall design. Every shoe type—whether athletic, formal, or casual—requires a specific last to achieve the right proportions.
Why Does the Last Matter?
- It determines the shoe’s overall fit, from the toe box to the heel.
- A poorly chosen last can distort the final pattern, causing discomfort and sizing inconsistencies.
- Factories rely on precise last measurements to maintain consistency across production.
Selecting the Right Last for Different Shoe Types:
- Sneakers & Running Shoes: Flexible lasts that allow for foot movement.
- Dress Shoes: Structured lasts with a sleeker shape for formal wear.
- Boots: Taller lasts that account for ankle support and shaft height.
- High Heels: Arched lasts that define heel height and foot posture.
A brand I worked with wanted to launch a chunky sneaker line but used a narrow dress shoe last for prototyping. The result? The midsole was completely misaligned, leading to costly revisions. The lesson? Choosing the right last is the foundation of a successful pattern.
Step #2 Preparing the Shoe Last for Pattern Making
Once you have the last, the next step is preparing it for pattern development. There are two main methods: manual pattern-making and digital pattern-making.
For Manual Pattern Making:
- Apply Masking Tape: Cover the last completely to create a working surface.
- Mark Key Construction Lines:
- Vamp Line: Where the toe box meets the upper.
- Instep Line: Center of the foot arch.
- Topline: Upper edge of the shoe opening.
- Heel Counter: Reinforced back portion of the shoe.
- Remove and Flatten: Carefully cut and remove the tape, laying it flat on paper to form the base pattern.
For Digital Pattern Making:
- Scan The Last: Use CAD software like Shoemaster, Romans CAD, or Rhino 3D.
- Digitally Map Out Key Lines: Ensure proportional accuracy and alignment.
- Convert Into Editable Pattern Pieces: Adjust seam allowances and fit details for production.
Step #3 Creating the Upper Pattern
The upper is the most visible part of the shoe—the material that wraps around the foot. A poorly designed upper leads to tight fits, wrinkles, or distortion during assembly.
Steps to Create the Upper Pattern:
- Trace The Taped Last: Transfer the outline onto paper or input it into CAD software.
- Add Seam Allowances: Typically 5–10mm, depending on stitching and material thickness.
- Mark Stitching Guides: Align components during assembly.
- Refine Curves & Symmetry: Ensure an even fit on both left and right shoes.
Always double-check symmetry. A small imbalance can lead to manufacturing defects, especially in mass production.
Step #4 Making the Sole Pattern
The sole pattern defines the shoe’s base shape, thickness, and material composition. If miscalculated, you’ll face fit problems, improper flexing, or weak adhesion points.
How to Create the Sole Pattern:
- Trace The Bottom Of The Last: Define the outsole shape.
- Adjust For Sole Thickness: Some materials like rubber and EVA foam expand slightly during production.
- Account For Heel Height: Crucial for high heels and wedges to maintain balance.
A brand I worked with underestimated the sole expansion rate of their rubber outsole. After production, the soles turned out wider than the uppers, causing a visible misalignment. We had to redo the entire mold. The takeaway? Always test your materials before finalizing patterns.
Step #5 Testing & Adjusting the Pattern
Even with precise pattern-making, testing is crucial before mass production. A single mistake at this stage can lead to hundreds or thousands of defective units.
How to Test Your Shoe Pattern:
- Create A Mock-Up: Use synthetic materials like EVA or PU leather for testing.
- Assemble A Sample Pair: Evaluate fit, comfort, and alignment.
- Identify & Adjust Common Issues:
- Tight Or Loose Fit: Modify seam allowances.
- Wrinkles Or Creases: Adjust stitching lines.
- Gaps Between Upper & Sole: Refine sole pattern thickness.
A well-made shoe pattern is the difference between a seamless production process and costly mistakes.
So, before sending your next design to production, ask yourself: Is your shoe pattern factory-ready?
3. Common Challenges in Shoe Pattern Making
A pattern maker’s first task is to examine the last selected by the designer. If the last is a familiar shape, marking the throat opening and collar height is a straightforward process. In many cases, the pattern maker already has a shell pattern on file—a template that represents a one-piece, seamless upper.
However, if the last is new, the pattern maker must create a fresh shell pattern using the taping method. This involves covering half the last with multiple layers of tape, carefully cutting along the centerline and bottom edge, and sketching the shoe design directly on the taped surface. Once the tape is removed and flattened, the initial pattern is complete.
Next, the pattern is digitized and cut from heavy paper for refinement. As a designer, you should always request a flat pattern for new designs. This allows for easier modifications—adjustments can be drawn directly onto a sample shoe and transferred back to the shell pattern for the pattern maker.
Modern production speeds up this process. Instead of shipping a sample shoe overseas for revisions, designers can scan and email corrections directly to the factory. This eliminates unnecessary delays, making the transition from concept to production faster and more efficient.
Have you faced any of these challenges before? What adjustments have helped improve your production process?
4. Difference Between a Shoe Designer and Shoe Pattern Maker
Shoe design and pattern-making are often mistaken as the same role, but they are two completely different skills. While a shoe designer focuses on style, branding, and market appeal, a pattern maker ensures that the design can actually be manufactured and worn comfortably.
So, what exactly does each role involve? Let’s break it down.
Aspect | Shoe Designer | Shoe Pattern Maker |
Primary Role | A shoe designer is responsible for the shoe’s overall look, materials, and branding. They focus on creating visually appealing designs that meet consumer demands. | A shoe pattern maker takes the designer’s vision and translates it into a precise technical pattern that fits the last and can be manufactured efficiently. |
Responsibilities | The shoe designer conceptualizes new footwear styles, selects materials and colors, and considers trends, customer preferences, and pricing. They often use 3D modeling or digital design tools to visualize their concepts. | The pattern maker examines the last, develops an accurate shell pattern, and ensures that each component is proportioned correctly. They refine patterns to match material properties, construction methods, and mass production standards. |
Required Skills | Creativity, trend awareness, and an understanding of materials and product performance are essential for a designer. They must also be able to communicate their ideas effectively through sketches or digital models. | A pattern maker must have strong technical skills, including precision in measurement, knowledge of shoe construction, and the ability to adjust patterns for different materials and manufacturing techniques. |
Tools Used | Designers typically work with sketchbooks, Adobe Illustrator, CLO 3D, or Rhino 3D to bring their ideas to life. | Pattern makers use tools such as measuring tape, rulers, grading scales, CAD software, and cutting tools to develop accurate patterns. |
Production Involvement | The designer is primarily involved in the initial design phase but does not handle the technical aspects of production. Their role is to create a compelling concept that aligns with the brand’s image. | The pattern maker works closely with manufacturers to ensure that the design is production-ready. They refine the pattern, solve fit issues, and adjust measurements based on material behavior. |
Do They Make Shoe Patterns? | A shoe designer does not need to create patterns but should be able to read, understand, and provide feedback on them. Their role is to ensure that the final product reflects their creative vision. | The pattern maker is responsible for developing and refining the shoe patterns, ensuring that all components align correctly for manufacturing and mass production. |
Collaboration | The designer provides creative direction and feedback on the shoe’s proportions, fit, and materials to ensure that the final product aligns with their vision. | The pattern maker takes the designer’s input and makes the necessary technical adjustments to ensure the shoe can be produced without defects or inconsistencies. |
Conclusion
A brilliant shoe design means nothing if it can’t be produced. That’s why pattern makers turn creativity into reality.
They transform sketches into precise, wearable, and manufacturable products. When designers and pattern makers work together, the result is a shoe that fits, lasts, and sells.
At XDS, we specialize in high-quality footwear manufacturing and help brands bring their designs to life.
Are your shoes production-ready? Let’s talk. Contact us today!